Before fitting the RHS rearset, as the original rearsets were Rizomas, they use a different actuating rod, spring, brake switch adjustable bolt, locking nuts
and pin to the stock rearsets, which won't work with the Gilles. In anticipation of this issue I pre-ordered these stock parts that will allow me to build up the RHS assembly.
As mentioned earlier, I had to dispense with both the billet reservoir and reservoir delete fairlead cover, as there is no clearance between the collector pipe and reservoir in this position, which if fitted, the heat from the exhaust would probably end up cooking the hydraulic fluid. I may look at other options but for now I will leave the stock setup.
There is a LOT going on here, including having to route and cable manage the two rear lambda sensors, rear wheel speed sensor, rear brake line, brake reservoir feed pipe and brake light switch, so that they don't foul on anything and as best as possible keep them away from contact with the exhaust. Hydraulic line to the rear master cylinder was secured using a Racebolt stainless banjo bolt torqued to 24.5Nm You might also spot the Pro Bolt M6 x 10mm reservoir bolt. As this is going into a brass threaded insert I opted to use 5Nm as a safe bet, since there is no figure given for it in the manual.
You will also obviously see the collector pipes and the main rear upswept pipe that has an enormous diameter, to which will attach the loop pipe and silencers. More on those later. This system is contortuous to put it mildly and needs a lot of adjustment to get it to fit right with still more tweaks to do once the rear sections are fitted, the rear subframe is back on and the support bracket is in place.
RHS rear set secured using 2 x Pro Bolt M8 x 20mm bolts torqued to 25Nm
As can be seen, there is not much room to play with! Spriing has about 5mm of clearance to the collector pipe, so all good.
Just waiting on one more small part to complete the RHS lower wiring, with just the front and rear loom branches to wire in, but before that I need to mount both front and rear subframes. Speaking of which, I decided to make a small change to rear subframe, the reason for which will become apparent once the frame is fitted back onto the bike.
Before that though I took the opportunity to fit the rear hugger and swing cover back on, as access to the bolts is easier without the subframe in the way. All retaining bolts torqued to 5Nm and a dab of Loctite 243. Don't be alarmed by the "Easy Rider" appearance of the exhaust at this stage. It will make a lot more sense when you see the rest of it in place.
Now back to the subframe. A little masking off required.
Then two coats of Ultra High Temp paint later and they look like this.
Once dry and the masking tape removed, I could apply some Parabond to the heat reflective foil area on both frame members, before securing the Lieb Speed carbon covers in place with zip ties as the bonding agent fully cures (in around 24 hours). The covers are not only secured to the subframe by bonding agent but in fact by four other bolts on each side. The reason for the bonding agent is to ensure the central area of the cover is as close a fit to the underlying subframe and cannot lift away from the surface.
The reason for the paint application will become clear later. That's all for tonight. Early shift at work in the morning, so I will try and post some more updates, later this week
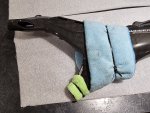