I recently noticed degradation of my very expensive, supposedly super strong stainless steel heel nut socket and, more importantly, the scuff marks it leaves on the rear wheel nut and the taper cone bush. This is after removing the rear wheel just six times. My current wheel nut and taper cone are OEM but I have an Aella taper cone on the way and I'm shopping for a (I think black anodised) rear wheel nut. So seeing the tough OEM items damaged (cosmetically) is not good news for prospective bling upgrades.
Today I posted a thread on the UK forum hoping to tap into the wealth of engineering expertise. Here's the thread...
www.ducatiforum.co.uk
As expected the feedback has been very helpful regarding the choice of an appropriate tool - wish I had asked before I bought one!
- but, also expected, no responses so far about how people avoid damaging delicate anodised and precious titanium components. So that seems like a good question for this forum where we have a strong interest in bling upgrades.
It's difficult to photograph but if you look carefully the left faces of the nut (which incur stress as we un-do the nut) are scuffed. And if you zoom on the photo you can see the face of the taper cone is scraped along the inside edge (closest to the nut) around the entire circumference.
In fact looking at the top-most right hand face (the tightening face) you can see it also has some slight scuffing. Removal of the nut is a moderately violent act using an impact wrench. But tightening is done relatively gently with a torque wrench.
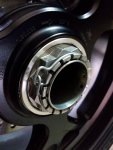
While the scuffing doesn't bother me and is hardly noticeable on the OEM nut and taper cone it would certainly stand out on polished titanium and would reveal bare aluminium on anodised surfaces.
So, those who have upgraded these components, how do you deal with this? Sooner or later you have to remove the rear wheel. How do you avoid damage? And which wheel nut socket do you use?
Today I posted a thread on the UK forum hoping to tap into the wealth of engineering expertise. Here's the thread...

Wheel Nut Socket - Am I Doing This Wrong?
Hoping to get advice from the experienced. My first Ducati and so my first experience with a 230Nm nut. Either my technique is lacking so I'm causing...
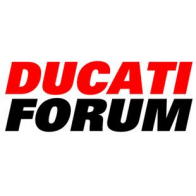
As expected the feedback has been very helpful regarding the choice of an appropriate tool - wish I had asked before I bought one!

It's difficult to photograph but if you look carefully the left faces of the nut (which incur stress as we un-do the nut) are scuffed. And if you zoom on the photo you can see the face of the taper cone is scraped along the inside edge (closest to the nut) around the entire circumference.
In fact looking at the top-most right hand face (the tightening face) you can see it also has some slight scuffing. Removal of the nut is a moderately violent act using an impact wrench. But tightening is done relatively gently with a torque wrench.
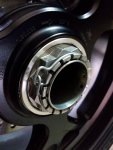
While the scuffing doesn't bother me and is hardly noticeable on the OEM nut and taper cone it would certainly stand out on polished titanium and would reveal bare aluminium on anodised surfaces.
So, those who have upgraded these components, how do you deal with this? Sooner or later you have to remove the rear wheel. How do you avoid damage? And which wheel nut socket do you use?